Cooling tower scale inhibitors are crucial components in industrial systems to maintain efficiency and prolong equipment life. As an experienced professional in the field, I've witnessed firsthand the transformative effects these inhibitors can have on operational productivity and cost-efficiency.
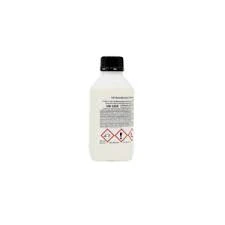
In the industrial sector, cooling towers are indispensable for managing and dissipating excess heat. However, these systems are prone to scaling, a common issue that significantly hampers performance. Scaling occurs when dissolved minerals in the water, such as calcium carbonate, precipitate and form a hard, insulating layer on heat exchange surfaces. This layer reduces heat transfer efficiency, leading to higher energy consumption and potential overheating, which can cause significant damage to the equipment.
The expertise in cooling tower scale inhibitors lies in their chemical composition, which is meticulously formulated to prevent mineral deposits. These inhibitors work by altering the crystal structure of the scaling minerals, thus preventing their adherence to surfaces. They can disperse already formed crystals, effectively turning potential scale into a manageable slurry, easily flushed out during routine maintenance.
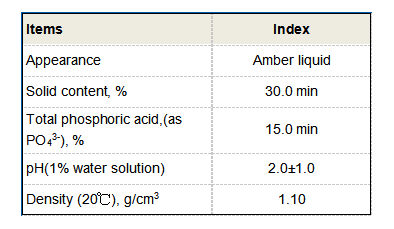
An authoritative approach to scale inhibition incorporates the latest technology and science-backed formulations. Modern scale inhibitors are developed through rigorous research and testing, ensuring they effectively handle specific scaling issues encountered in different industrial environments. For example, polycarboxylates, phosphonates, and certain polymers have been identified as potent scale inhibitors due to their high tolerance to varying pH levels and temperatures.
cooling tower scale inhibitor
Furthermore, it's essential to trust in products that adhere to industry standards. Reliable inhibitors are those that not only meet industry regulations but also undergo continuous third-party testing for performance validation and environmental safety. This establishes a strong foundation of trust with users, as they can rely on the inhibitors to deliver consistent results without adverse environmental impacts.
In practice,
implementing an effective scale inhibition system can lead to substantial benefits. I recall a case study involving a large manufacturing plant that struggled with frequent downtime due to scaling issues in their cooling towers. By switching to a high-quality scale inhibitor, expertly chosen to match their water chemistry, the plant not only reduced maintenance downtime by 30% but also observed a decrease in energy costs by up to 15%.
Such experiences underscore the importance of selecting the right product tailored to specific needs, highlighting the expertise required to optimize industrial cooling systems effectively. In conclusion, scale inhibitors are not just a preventive measure; they are a strategic investment in operational efficiency, driven by a blend of experience, technical knowledge, authority in chemical management, and a commitment to trustworthy practices. Making informed choices in this area not only improves immediate system performance but also contributes to longer-term sustainability and cost savings.