Integrating a high-quality scale and corrosion inhibitor into your cooling tower system can significantly enhance its performance, preventing costly damages and inefficiencies. Cooling towers play a crucial role in industrial operations, including power plants, manufacturing facilities, and HVAC systems. They manage heat by transferring it from machinery and equipment to the environment, using water as the primary cooling medium. However, these systems are vulnerable to scale and corrosion, two persistent challenges that can diminish their effectiveness.

Scale formation occurs when mineral deposits, such as calcium carbonate and magnesium silicate, accumulate on the surfaces of the cooling tower. This accumulation restricts water flow and reduces heat transfer efficiency. It's akin to cholesterol build-up in the human body, where blocked arteries can lead to heart problems. Similarly, scaled cooling towers consume more energy and may require costly repairs or replacement parts.
In contrast, corrosion is the gradual degradation of materials due to chemical reactions with environmental elements. In cooling towers, corrosion primarily affects metal components because of their exposure to water and oxygen. The result is weakened structures and potential system failures. Left untreated, corrosion can severely compromise the integrity of the entire cooling system.
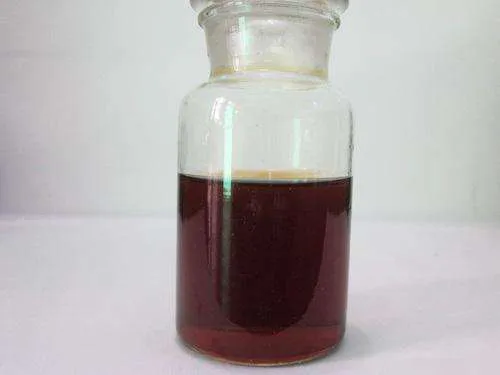
High-performance scale and corrosion inhibitors are engineered to tackle these challenges head-on. They are formulated using a blend of chemicals that target specific factors contributing to scale and corrosion. Some inhibitors leverage a phosphate-based formula to prevent scale by stabilizing mineral particles in the water, thereby preventing them from forming deposits. Others use polymer-based technology, which creates a protective barrier on metal surfaces that resist corrosive substances.
scale and corrosion inhibitor for cooling tower
When selecting a scale and corrosion inhibitor for your cooling tower, consider one developed from rigorous research and testing. Look for products endorsed by field experts and legal certifications that prove their efficacy and safety. Peer-reviewed studies and testimonials from other industry professionals can provide insight into the product’s performance in real-world scenarios. This trustworthiness is paramount when making an investment destined to protect your infrastructure.
Moreover, the expertise of professional water treatment consultants can be invaluable. These professionals conduct routine system evaluations and suggest tailored inhibitor treatments that meet specific operational needs. Customized solutions not only extend the lifespan of the cooling tower but also optimize its efficiency and minimize environmental impact, resulting in significant cost savings over time.
Incorporating scale and corrosion inhibitors into a preventative maintenance plan ensures long-term operational reliability. Regular monitoring coupled with these specialized chemical agents maintains heat exchange efficiency and prevents unplanned production downtimes. As the global industry environment becomes increasingly competitive, businesses that prioritize infrastructural health stand to gain a significant advantage.
In conclusion, the strategic application of scale and corrosion inhibitors in cooling tower systems is essential for maintaining peak operational efficiency and safeguarding capital investments. By embracing cutting-edge technology, backed by authoritative expertise and credibility, businesses can mitigate the risks associated with scale and corrosion, achieving a seamless, sustainable operational process.